Unwrapping the Differences: Cast Pallet Wrap vs. Blown Pallet Wrap
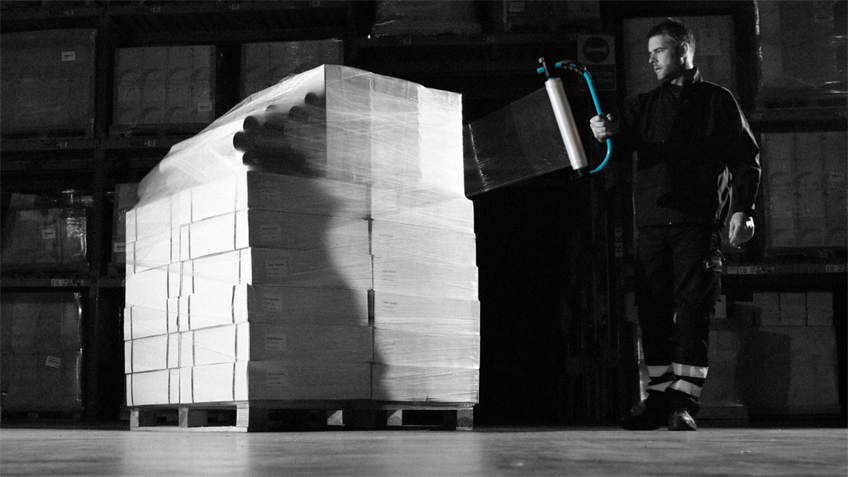
Published date: 17 August 2023
When it comes to securing and protecting goods for transportation and storage, pallet wrap has become an essential tool in various industries. However, not all pallet wraps are created equal. Two prominent contenders in the world of pallet wrapping are cast pallet wrap and blown pallet wrap. While they serve the same fundamental purpose – safeguarding products during transit – they differ in terms of manufacturing processes, characteristics, and application techniques. In this blog, we will delve into the distinctions between these two types of pallet wrap to help you make an informed choice for your packaging needs.
Manufacturing Processes
The primary dissimilarity between cast and blown pallet wrap lies in their manufacturing processes, which greatly influence their properties and performance.
Cast Pallet Wrap:
Cast pallet wrap, also known as cast stretch film, is manufactured using a process called cast extrusion. In this method, the polymer is melted and then extruded through a flat die onto a chill roll. As it cools down rapidly, the film solidifies. This process results in a thinner, quieter, and more transparent film compared to blown pallet wrap.
Blown Pallet Wrap:
Blown pallet wrap, also referred to as blown stretch film, is produced through blown extrusion. In this method, the polymer is melted and then pushed through an annular die, creating a bubble-like structure. This bubble is then cooled using air, stretched, and eventually flattened into a film. The blown process lends the film more resilience and strength, making it a suitable choice for heavy or irregularly shaped loads.
Characteristics and Performance
Cast Pallet Wrap Characteristics:
Clarity: Cast pallet wrap is exceptionally clear, allowing for easy identification of packaged products and barcodes.
Quietness: Due to its smooth and thin nature, cast wrap produces less noise during application.
Stretch-ability: Cast film offers excellent stretch and cling properties, adhering closely to the load's contours.
Tear Resistance: While cast wrap is generally less tear-resistant than blown wrap, it compensates with its other advantageous characteristics.
Cost: Cast pallet wrap is typically more cost-effective than blown wrap, making it a popular choice for everyday packaging needs.
Visit our Cast Pallet Wrap range today !
Blown Pallet Wrap Characteristics:
Strength: Blown pallet wrap is known for its superior strength and resistance to punctures, making it ideal for heavy loads or sharp-edged items.
Load Stability: The robust nature of blown film ensures enhanced load stability, minimizing the risk of shifting or damage during transit.
Thickness: Blown film is generally thicker than cast film, contributing to its higher tear resistance.
Noise: The blowing process can result in a noisier unwrapping experience due to its slightly rougher texture compared to cast film.
Cost: Blown pallet wrap is often more expensive due to its manufacturing process and enhanced characteristics.
Visit our Blown Pallet Wrap range today !
Application Techniques
Both cast and blown pallet wraps can be applied using similar techniques, such as hand wrapping, machine wrapping, or utilizing specialized dispensers. However, the choice of film depends on the specific requirements of the load and the desired level of protection.
In the realm of packaging and shipping, selecting the right pallet wrap is a critical decision that can significantly impact the safety and integrity of your products. Cast and blown pallet wraps have distinct characteristics stemming from their manufacturing processes, and each excels in different scenarios. Cast wrap's cost-effectiveness, clarity, and stretch-ability make it a great choice for various applications. On the other hand, blown wrap's strength, tear resistance, and load stability make it the preferred option for heavy or irregularly shaped loads. By understanding these differences, you can make an informed choice that aligns with your packaging needs and budget constraints, ensuring that your goods reach their destination securely and in pristine condition.
Comments
There are currently no comments, be the first to comment.